Well, lemme tell ya about fireclay refractories. This stuff here, it’s somethin’ real special for anyone who’s lookin’ to deal with high heat, y’know? See, fireclay, it’s a type of clay that’s got a knack for holdin’ up in some pretty scorchin’ temperatures. Not like yer regular mud or dirt—oh no, this here’s got somethin’ in it called alumina, makes it real tough and heat-lovin’. Folks use it in all kinds of places, like them big ol’ furnaces and kilns where ya need stuff that won’t melt away in a blink.
Now, makin’ these fireclay refractories, that’s a bit of a process, ain’t as simple as just diggin’ up some dirt and throwin’ it in the fire. They got steps, see, and every one of ‘em’s important if ya want that clay to do its job right. So, lemme break it down simple-like:
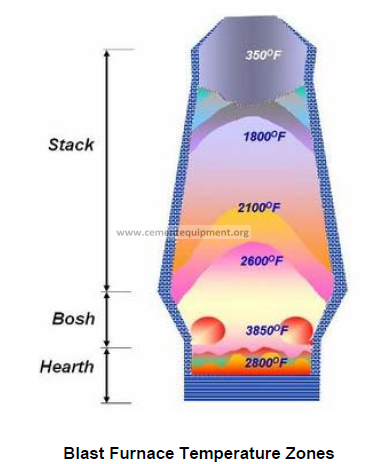
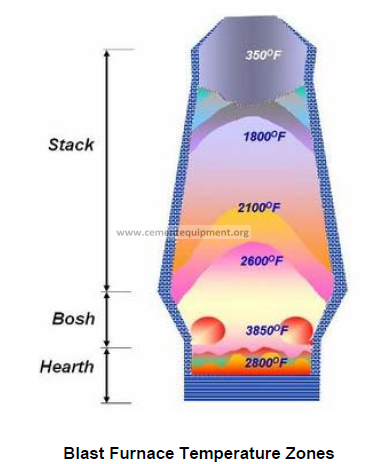
Step 1: Gettin’ the Raw Stuff Ready
First thing ya do, ya gotta get that clay all ground up nice and fine. Some folks call it crushin’ and grindin’—whatever ya call it, it’s all ‘bout makin’ the clay powdery, like flour. Sometimes ya even gotta heat it a bit, dry it out too. Makes it easier to work with later on. And it ain’t just one type of clay, no, they got a mix—things like chamotte and flint clay get thrown in too. Real fancy names, but don’t let ‘em fool ya; they’re just good ol’ heat-lovin’ clays too.
Step 2: Makin’ the Shape
Once that clay’s all nice and ground up, next thing ya gotta do is shape it. Now, this here ain’t like shapin’ cookies, no sir. They put the clay in molds, press it down real hard. Sometimes they even add a lil’ water, makes it stick together better. They wanna make sure it comes out lookin’ like a brick or whatever shape they need, nice and sturdy.
Step 3: Fire It Up
This here’s where the magic happens, I tell ya. They take them shaped-up clay pieces and put ‘em in a big ol’ kiln, hotter than the hottest summer day you ever felt. And it ain’t no quick process—this part takes time. They call it “firing.” The heat hardens the clay up real nice, makes it ready to take on even more heat later on. They got these big ovens reachin’ way up in temperatures, and that’s what makes the clay go from soft stuff to rock-solid bricks.
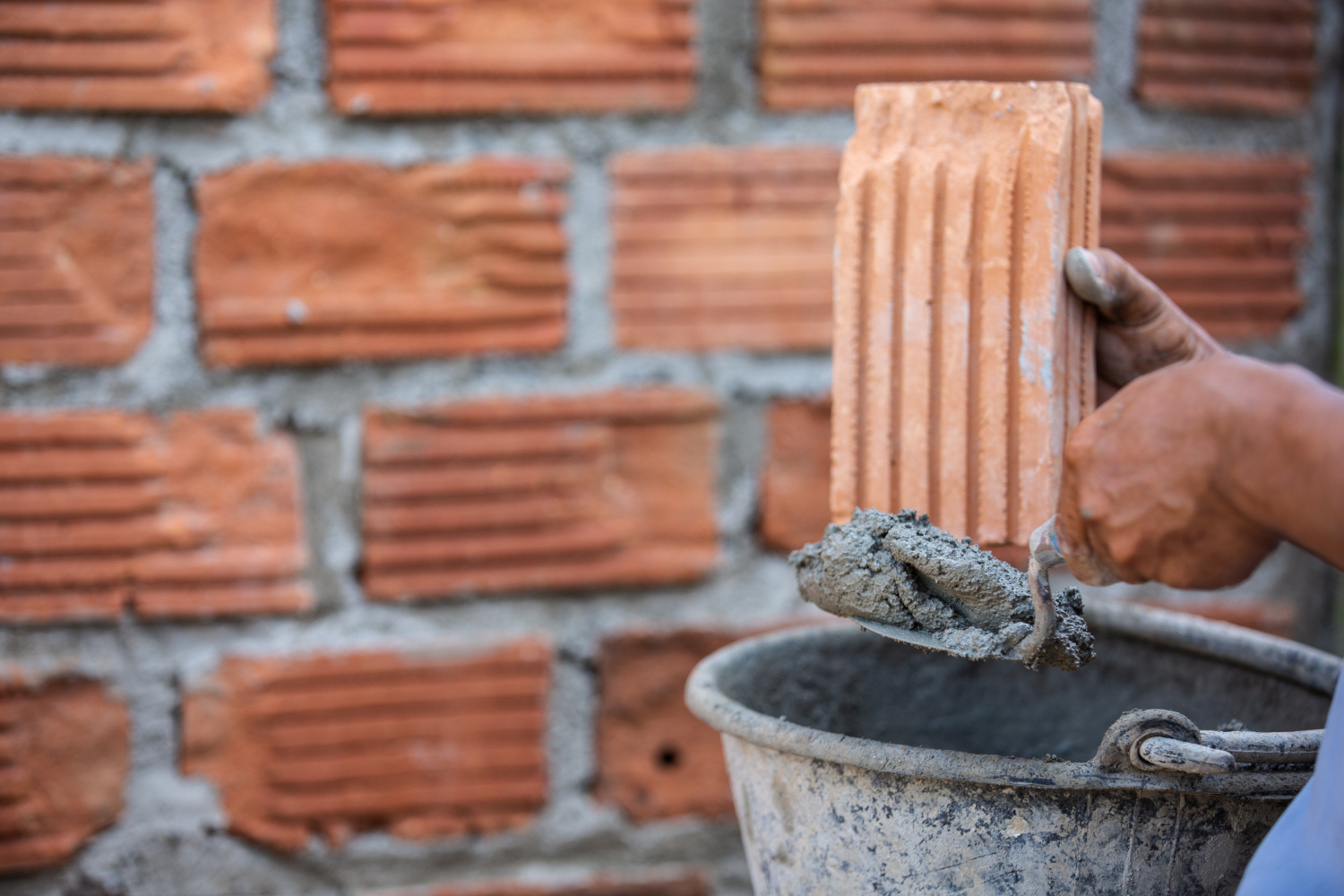
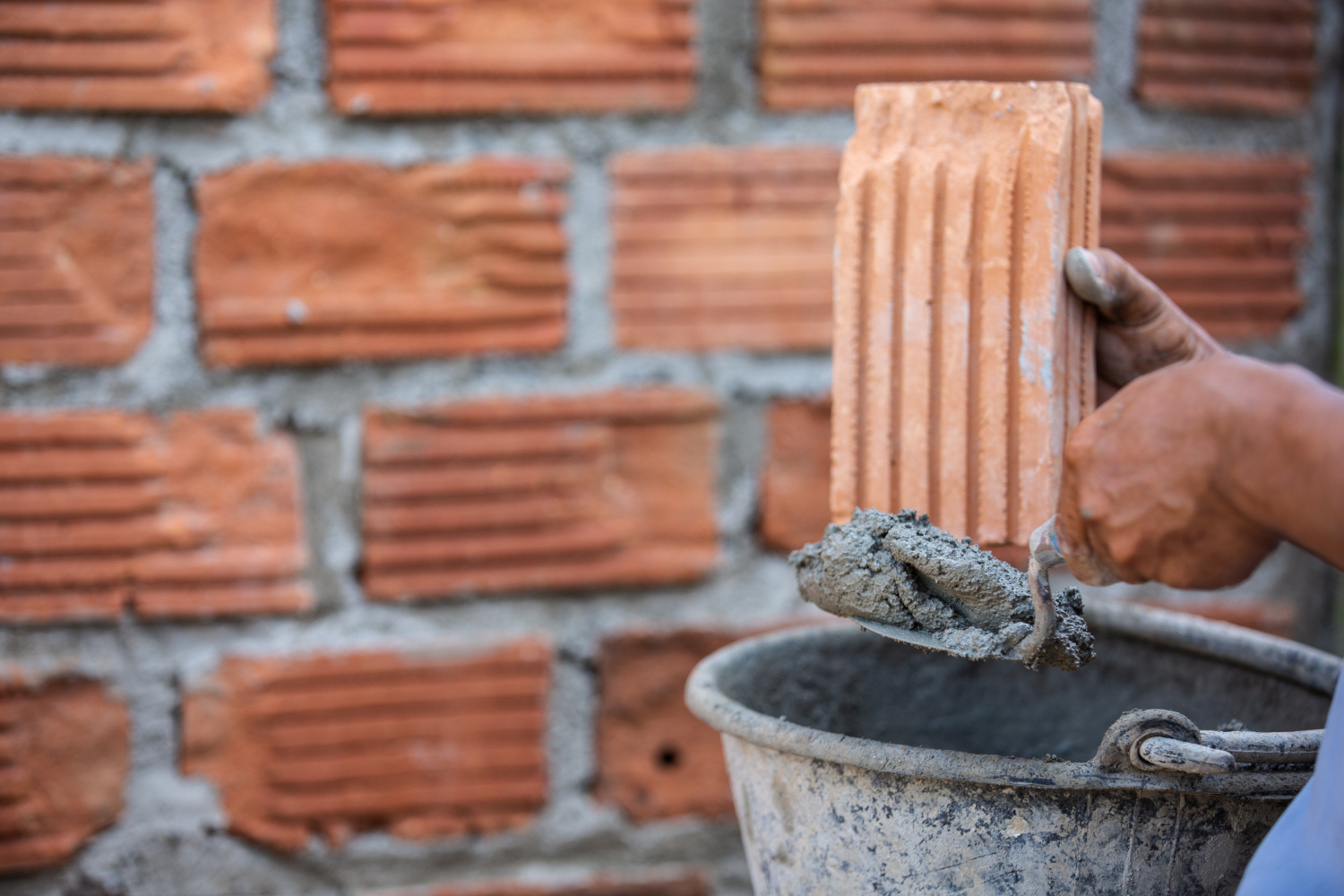
Step 4: Finishing Touches
Last step, they give it a lil’ polish, check it for cracks and holes. Anything that don’t look strong enough, they toss it out. Ya gotta have perfect bricks, or else when it hits the heat, it’s gonna crumble. They might even give it a coat or somethin’ special so it stays tough and don’t wear out too quick. Then, it’s all set and ready for the furnace or wherever else they’re gonna use it.
So, why folks love fireclay refractories, you ask? Well, lemme tell ya, these things are strong as an ox, can take heat like nobody’s business, and don’t crack easy. They’re used a whole lot in places where folks need real heatproof materials—like iron and steel factories, glass-makin’ plants, you name it. If there’s fire involved, chances are they’re usin’ fireclay bricks to keep things from meltin’ down.
And fireclay itself, it’s a natural thing. Comes right outta the ground, gets a lil’ help from folks who know what they’re doin’, and then it’s ready to stand up to some mighty high heat. Not just good for bricks, either; folks use it in ceramics, insulation, and even pottery sometimes. But when it comes to real heavy-duty stuff, it’s them fireclay refractories that folks are after. They last long and they don’t give up easy.
So, next time ya hear about fireclay or them fireclay bricks, ya know it ain’t just regular ol’ clay. It’s tough stuff made for tough jobs, helpin’ keep things safe and steady in some real hot places. Strong, reliable, and all-natural—ain’t that somethin’?
Tags:fireclay, refractories, heat-resistant materials, refractory bricks, manufacturing process
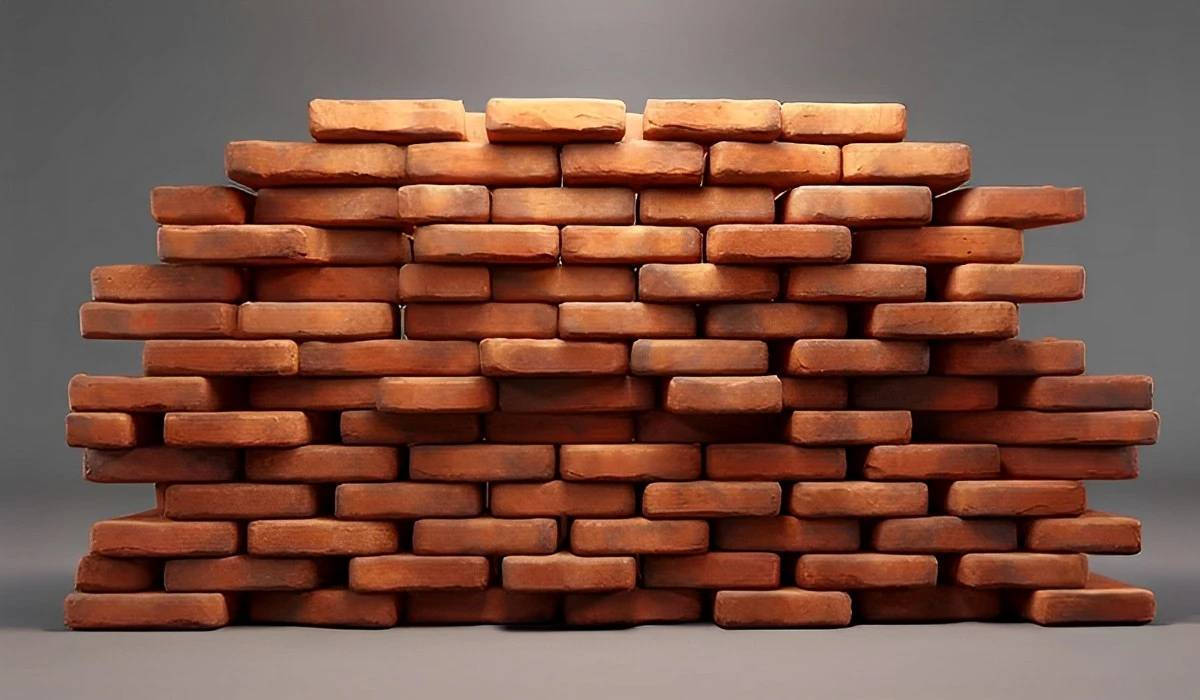
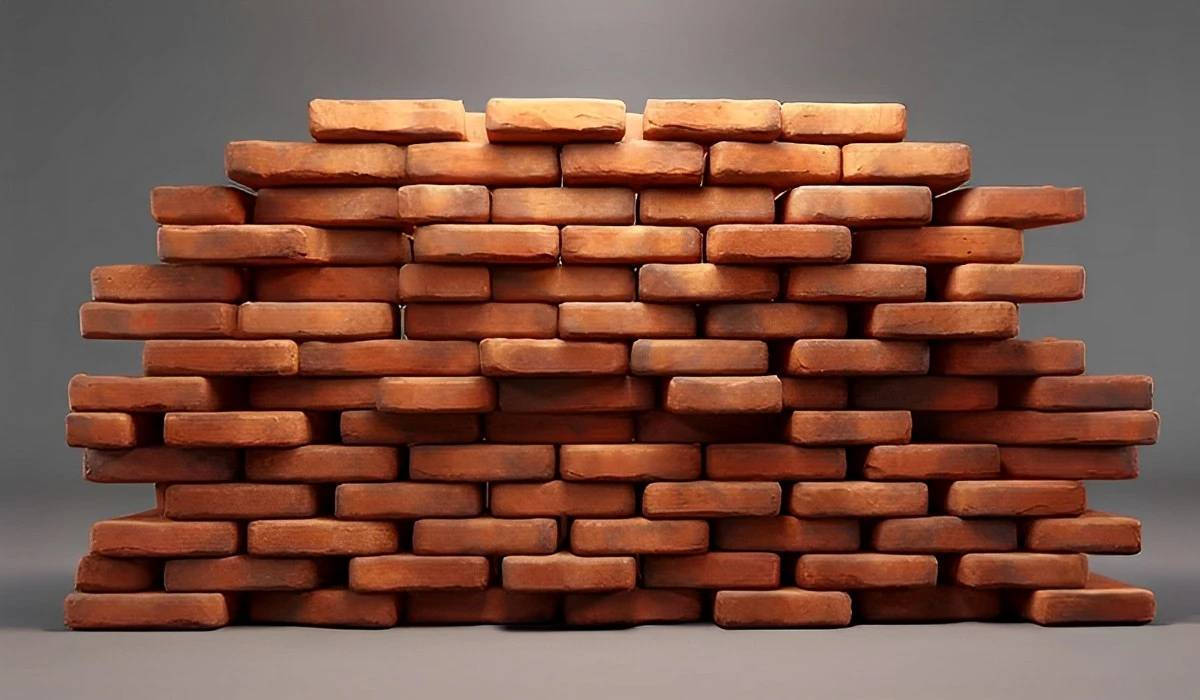